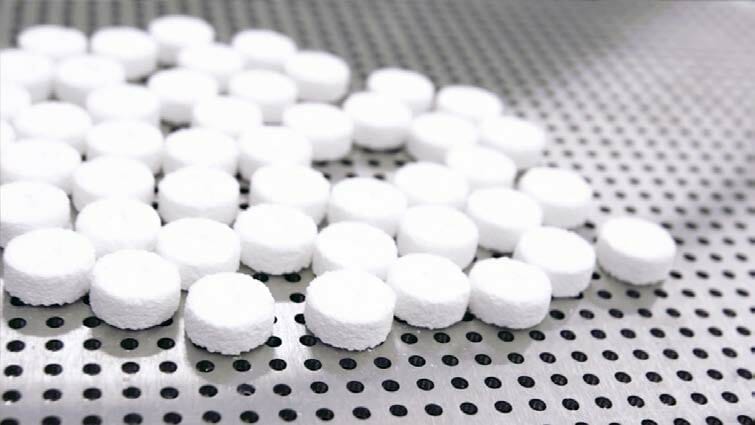
Additive Manufacturing: 3D-Printed Pills
Case Studies, Resources | March 20, 2020
Last updated on March 20, 2020
Certain medical conditions such as epilepsy need to be treated with high doses of medicine, but many patients are unable to swallow large pills. 3D printing can address this problem by packing more medicine into each pill and by creating a pill structure that dissolves in a patient’s mouth with a single sip of water, so it does not need to be swallowed whole.
THE PROBLEM
Traditionally, many patients who need high doses of medicine have to take more than one pill. But increasing the number of pills decreases the chances of patients sticking to the course of treatment. They might not want to take more than one pill, or miscount. To address this problem, pharmaceutical companies try to pack as much medicine as possible into one pill, manufacturing large tablets or capsules. Unfortunately, some patients with epilepsy, especially children, have trouble swallowing such large pills. Liquid suspensions are an alternative, but they often have to be taken multiple times a day and dosing with a syringe is not always precise. Such patients need something that is easy to swallow and delivers a big dose of medicine.
Conventional tablet manufacturing techniques are ineffective on both fronts. For example, a popular freeze-drying technique known as Zydis limits how much medicine can be loaded onto a tablet. Another method, known as soft compression, has the same problem, with the additional complication that the tablets don’t disperse easily in patients’ mouths even when swallowed with water.
APRECIA’S SOLUTION: 3D-PRINTED PILLS
3D printing addresses the dual problems of dosage and ingestibility.
Pharmaceutical company Aprecia 3D-prints levetiracetam, a medicine for epilepsy, as an easily dispersible (and then swallowable) pill it sells under the brand name Spritam.
The modified 3D printing process
Aprecia uses a common 3D printing technique called binder jetting. In traditional binder jetting processes, a powder is spread in a thin layer on a platform and an inkjet printer moves over the layer to glue the powder together. This action repeats over and over until the desired thickness is printed.
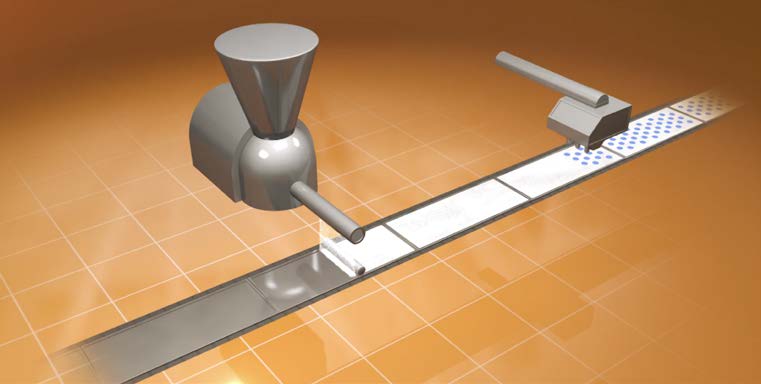
The 3D printing process for ZipDose pills. View full video here. Image courtesty of Aprecia Pharmaceuticals, LLC
- A powdered blend is deposited as single thin layer on a platform.
- A binding fluid is deposited to bind the powered blend together.
- Repeat 1 & 2 several times to add more layers based on the dosage to form a pill.
Aprecia manufactures Spritam by spreading the powdered medicine in a thin layer and precisely placing tiny droplets of polymer solutions to bind the powder together. These droplets are generated using industrial grade inkjet printer nozzles. After the pill is printed, it is dried at 50–60°C to remove moisture and sealed in child-resistant blister packaging.
The improvements
The finished pill disperses in the mouth within about 10 seconds and packs up to 1000 mg of the medicine. Until now, this much medicine would require a large tablet that is difficult to swallow, or come in a liquid form that is inconvenient to administer and store.
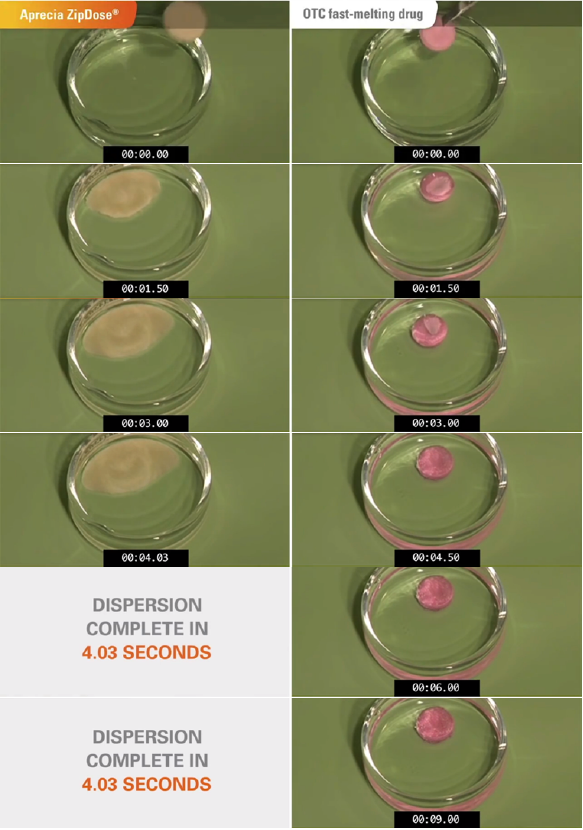
A comparison of the dissolve times in water for an Aprecia ZipDose pill versus a typical over-the-counter option. View full video here. Image courtesy of Aprecia Pharmaceuticals, LLC
CHALLENGES
Producing the 3D-printed pills at scale involved a number of challenges, a few of them specific to the pharmaceutical industry.
Increasing print speed
One of the main limitations of 3D printing can be speed. A conventional tablet press can yield hundreds of thousands of tablets per hour, but “inherently, when you’re building things layer by layer, it’s a slower process,” says Jaedeok Yoo, chief technology officer at Aprecia. Yoo’s doctoral research at the Massachusetts Institute of Technology in 3D printing formed the basis for the Spritam solution.
Conventional 3D printing follows an alternating process: deposit, fuse, deposit, fuse. The platform holding the powder bed is stationary, with the print head and the fusing mechanism taking turns performing their functions. Aprecia’s approach inverts this technique. It keeps the powder-spreading and the droplet-dispensing mechanisms stationary and moves the base platform instead. By moving the platform in a continuous “racetrack” configuration, Aprecia eliminates a lot of time spent waiting for each mechanism to perform its elaborate dance. The Aprecia 3D printing solution continuously dispenses the medicine while simultaneously depositing the binder droplets.
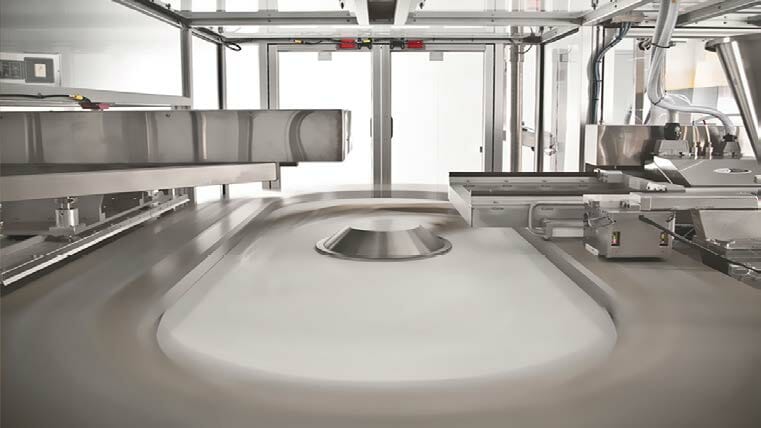
The print bed “racetrack,” which passes under the print head and fusing mechanism on the right. An additional layer is added to each time a pill circles the racetrack until the printing is complete. Image courtesy of Aprecia Pharmaceuticals, LLC
Aprecia’s accelerated 3D printing process produces tens of thousands of units per hour, as opposed to the 10–100 tablets per hour that the prototype could make, improving efficiency by orders of magnitude.
Optimizing pill design and formulas
The team at Aprecia experimented with medicine-to-filler ratios to determine what would work best. Yoo says, “As part of the development process, we’d be looking at different types of binding agents and amounts. Because these tablets are supposed to disperse in the patient’s mouth, we have to make sure it tastes acceptable and is not bitter. If it is a bitter drug, we have to make sure the bitterness is masked out appropriately.”
The finished pill needed to be rugged enough for transport. It also had to disperse quickly with a sip of water but not dissolve in the palm of the hand. Also, the print head depositing the binding agent needed to be precise, so Aprecia tested many different 3D-printed formulas before arriving at a final version.
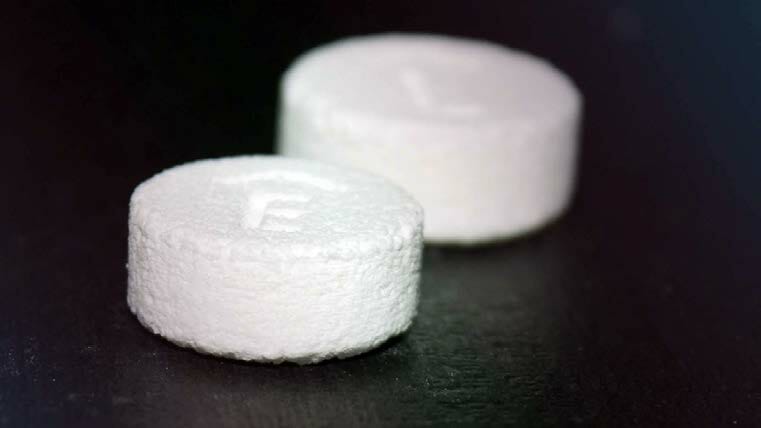
With the help of 3D printing, dosage pills can be designed and built with a porous structure that allows liquid to quickly dissolve it, but still smooth enough for a pleasant texture. Image courtesy of Aprecia Pharmaceuticals, LLC
Securing FDA approval
Approval from the Food and Drug Administration was another hurdle. Preparing for the FDA approval process was as difficult as the actual interaction with the FDA. Different regulatory experts had differing perspectives on how the FDA might react, Yoo says.
The FDA requires that companies follow regulations to ensure the safety, identity, strength, quality, and purity of manufactured products. At the end of the binder jetting process, loose, unbound powder surrounds the 3D-printed objects. Additive manufacturing companies, including Aprecia, typically collect this powder and recirculate it into the process. Both Aprecia and FDA wanted to ensure that this recirculation step yields batches of pharmaceutical products with consistent quality. Aprecia validated the Spritam manufacturing process, which has been approved by the FDA.
RESULTS
Feedback from patients and caregivers has been positive, Yoo says. As one example, the mother of a 9-year-old appreciates that her daughter can take Spritam with just a sip of water. Previously, her daughter relied on an oral solution that had to be measured and administered multiple times using an oral syringe. Thus far, Spritam has been promoted only in select regional test markets. Based upon the response, Aprecia plans to increase promotion in 2020.
IMPLICATIONS
3D printing can provide alternatives when traditional methods of pill manufacturing don’t deliver desired results.
When to use 3D printing in pharma
Because additive manufacturing is a relatively new technology, it is not as price competitive as conventional techniques. Pharmaceutical companies need to weigh commercial factors—including the size of the patient population, market reach, and dosage forms—to determine if this approach will be profitable. Products that contain large amounts of medicine or that have extremely bitter active ingredients may be the best bets. 3D printing may also work for drugs that will benefit underserved patients with rare diseases and medical conditions.
3D printing’s promise beyond drug manufacturing
Additive manufacturing may be useful to the pharmaceutical industry in other ways too. It can accelerate the development of new medical compounds, because companies can rapidly prototype and test different doses and delivery methods. Cutting development time can save significant amounts of money, inasmuch as the cost to develop a new prescription medicine is very high. (It was $2.6 billion in 2014, according to a study by the Tufts Center for Drug Development, and is growing at 8.5% annually.) 3D printing also may allow patients to access life-saving drugs more quickly.
This article was developed by MIT Horizon, an initiative to help organizations and working professionals learn about emerging technologies like additive manufacturing, AI and robotics. To learn more about MIT Horizon, please visit our website at https://horizon.mit.edu or contact us at [email protected].